Repair And Maintenance Of Grain-Rough Separation Equipment
1. Regularly check the equipment: Regularly check the various parts of the grain separator equipment, including the transmission device, screen and roller, etc. Make sure they are not loose, worn or otherwise damaged. If any problems are found, repair or replace them in time.
2. Clean the equipment: Due to frequent use, the grain-rough separation equipment is prone to accumulate a lot of grain and dust. Therefore, it is very important to clean the equipment regularly. You can use a soft brush or compressed air to remove impurities on the screen, and rinse the inside and outside of the equipment with clean water.
3. Lubricate parts: The transmission device and roller parts in the grain-rough separation equipment need to be kept in good lubrication. During the repair and maintenance process, these parts should be regularly filled with an appropriate amount of lubricating oil or grease to reduce friction and wear and improve the working efficiency of the equipment.
4. Maintain a good working environment: The paddy separator machine should be placed in a dry and clean place to avoid moisture or dust pollution. At the same time, it is also necessary to maintain good ventilation around the equipment to prevent the equipment from overheating.
5. Routine maintenance: In addition to regular inspection and cleaning, some routine maintenance work is also required, such as tightening screws, adjusting the tension of the transmission device, etc. These simple tasks can help maintain the stability and normal operation of the equipment.
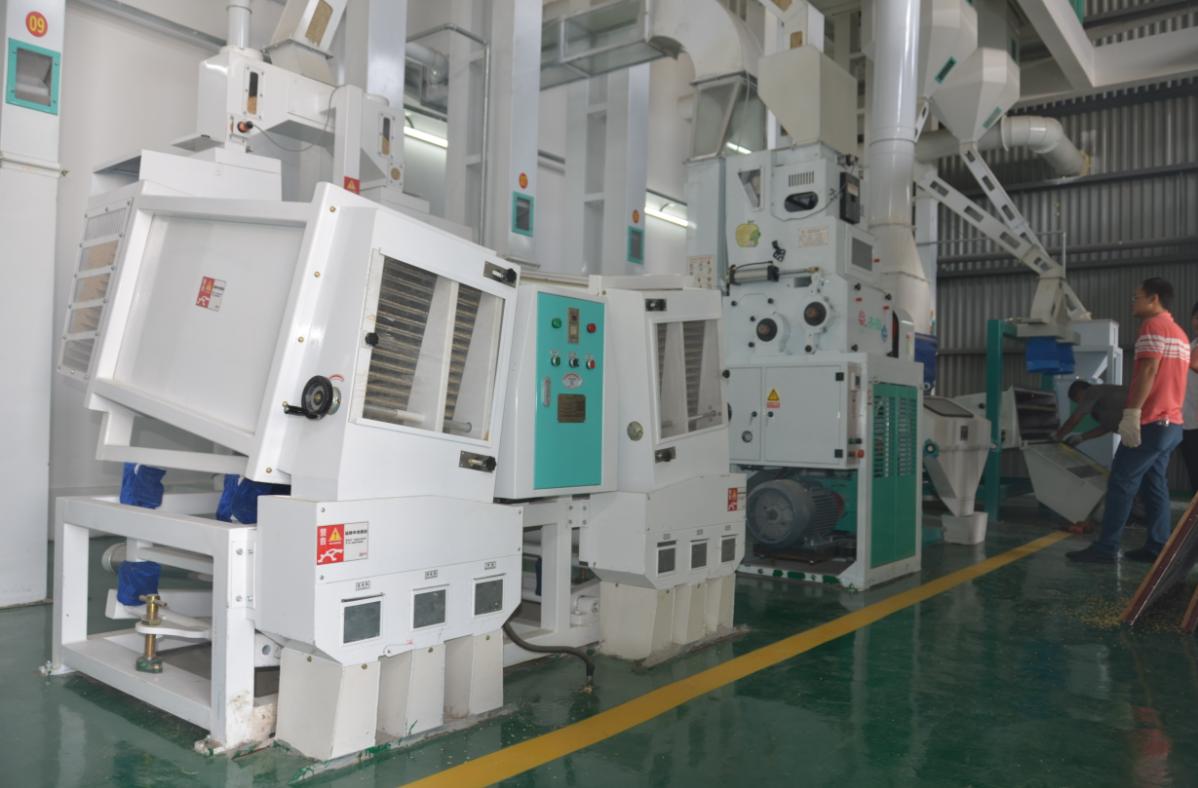
Production Process Of Grain-Rough Separation Equipment
First, the production process of paddy separator equipment includes two main steps: cleaning and pretreatment. Cleaning refers to cleaning the raw grains to remove impurities and dirt attached to the surface to ensure the normal operation of the separation equipment and the sanitation and safety of the products. Pretreatment is to preheat or steam the cleaned raw materials to soften the raw materials and improve the separation effect.
Secondly, the core technology of grain-rough separation equipment is to separate brown rice and grains through different physical methods. Common separation methods include vibration screening, airflow sorting and gravity separation.
Among them, vibration screening uses the vibration of the screen to make the brown rice fall off from the grains, while the grains are retained by the screen; airflow sorting uses the effect of airflow to make the brown rice and grains produce different movement trajectories under the action of gravity, thereby separating the brown rice and grains; gravity separation uses the density difference between brown rice and grains to separate them by gravity.
Finally, the maintenance and cleaning of the equipment should be paid attention to in the production process of the grain-brown separation equipment. Regular maintenance and maintenance of the equipment, timely replacement of wearing parts, to ensure the normal operation of the equipment; in addition, the equipment needs to be thoroughly cleaned after each use to remove residues to avoid affecting the next production.
Precautions For Grain-Brown Separation Equipment
1. Safe operation of equipment: Before using the grain-brown separation equipment, it is necessary to ensure that all safety equipment and protective devices have been installed and the employees must be trained and understand the operation manual of the equipment. Operators should wear appropriate personal protective equipment, such as helmets, goggles and earplugs.
2. Equipment maintenance: Regular maintenance of equipment is the key to ensure its normal operation and extend its service life. Clean the surface of the equipment, remove accumulated materials, and check whether the fasteners of the equipment are loose or damaged. Lubricate mechanical parts regularly to ensure their flexible operation, and pay attention to replacing worn parts.
3. Adjustment and calibration: Before using the grain separation equipment, the equipment needs to be adjusted and calibrated to adapt to different types and specifications of grains. Make sure that the height and speed of the equipment's trays and conveyor belts match the grains being processed to achieve efficient separation.
4. Avoid overload operation: The operating speed of the grain separation equipment should be adjusted according to the load of the equipment. Too high speed will cause equipment blockage and rapid wear of wearing parts, while too low speed will affect production efficiency. Make sure that the equipment is reasonably calculated and adjusted for load to avoid overload operation.
5. Regular inspection of equipment: It is essential to regularly check the operating status of the equipment. Check whether the equipment has abnormal noise, resonance or vibration. Check whether the electrical and hydraulic systems are working properly, and repair any faults or damage in time.
6. Shutdown for maintenance: Always shut down the equipment when repairing, cleaning and replacing parts. Ensure that the equipment is completely stopped and the power is cut off to prevent accidental injuries and equipment damage.
7. Train operators: All operators should receive relevant training and understand the operation and maintenance knowledge of the equipment. The training content should include the normal operating procedures of the equipment, emergency shutdown procedures, and common troubleshooting methods.
Troubleshooting Of Grain Separation Equipment
First, one possible fault is the blockage of the feed port of the equipment. When too much grain accumulates at the feed port, it will cause feed obstruction and affect the working effect of the equipment. For this problem, we can take the following troubleshooting methods: First, turn off the power of the equipment, and then clean up the accumulation around the feed port. During the cleaning process, be sure to pay attention to safety and avoid injury.
Secondly, the equipment may have a grain overflow fault. This is usually caused by excessive feed volume or insufficient processing capacity of the equipment. To solve this problem, we can appropriately reduce the feed volume and control it within the tolerance range of the equipment.
In addition, we can also consider upgrading the equipment or increasing the number of equipment to meet a larger processing volume. In addition, the motor of the equipment may fail, resulting in poor separation effect or failure of the equipment to operate normally. When we detect abnormal noise or heating of the motor, we should shut down the device in time and check whether the wiring of the motor is loose and whether the voltage is normal. If the problem persists, the motor may need to be replaced or repaired.
Finally, a common fault that the device may encounter is unstable operation. This may be caused by an unstable base or loose installation of the device. To solve this problem, we can adjust the support screws of the base of the device to ensure that the device can be firmly installed on the ground. In addition, we can also check whether the transmission parts of the device are loose and tighten them in time.
Post time: Jan-14-2025